Optimieren Sie ein Druckluftsystem mit stark schwankendem Luftbedarf
Abstrakt
Wenn ein Druckluftsystem große Luftmengen benötigt (ca. >100 m3/min) und der Luftbedarf im Laufe des Tages stark schwankt, sind die Endverbraucher der Meinung, dass große Schraubenkompressoren mit variabler Drehzahl erhebliche Einsparungsmöglichkeiten bieten, indem sie den Druckluftstrom genau an den Bedarf des Systems anpassen.
Betrachten wir als Beispiel den in Abb. 1 dargestellten Fall. Die Studie vergleicht den Energieverbrauch von sechs alternativen Lösungen in Bezug auf die Anzahl der installierten Kompressoren, die Größe der Kompressoren und die Art der Verdichtungstechnologien (d. h. ölfreie Zentrifugal- und ölfreie Rotationskompressoren), wenn der tägliche Durchflussbedarf eine Variabilität von bis zu 90 % des maximalen Luftbedarfs aufweist.
Abb. 1: Durchflussprofil mit hoher Variabilität (90 Prozent) für einen 24-Stunden-Zeitraum.
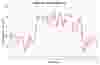
Der Einfluss des Steuerungssystems eines Luftkompressors und seiner verschiedenen Steuerungslogiken wird bei der Analyse ebenfalls berücksichtigt.
Der Energieverbrauch derselben sechs Lösungen wird dann mit verschiedenen Luftbedarfsmustern verglichen, um das Verhalten der sechs Systeme bei schwankendem Produktionsbedarf zu simulieren (d. h. es werden auch vier andere tägliche Luftbedarfsmuster mit unterschiedlicher Variabilität berücksichtigt).
AUSWAHL DER RICHTIGEN DRUCKLUFTLÖSUNG
Es gibt verschiedene Kompressionstechnologien, und jede kann ihre eigenen Vor- und Nachteile haben, abhängig von der jeweiligen Anwendung, dem Betriebsbereich, der Leistung, der Kapazität und anderen Aspekten.
Wenn ein Druckluftsystem jedoch große Luftmengen benötigt und der Bedarf im Laufe des Tages stark schwankt, sind die Endnutzer häufig der Meinung, dass nur der Einsatz großer Schraubenkompressoren mit variabler Drehzahl große Einsparungen ermöglichen kann, indem der Durchfluss der gelieferten Druckluft genau an den Bedarf des Systems angepasst wird.
Ziel dieser Studie ist es, sechs verschiedene Druckluftlösungen zu vergleichen und zu bewerten, wenn der Luftbedarf stark schwankt. In der Studie wurden fünf variable Strömungsprofile, wie in den Abbildungen 1 bis 5 dargestellt, berücksichtigt, um einige Leitlinien zu definieren, die den Endnutzern helfen sollen, das beste System für ihre Anwendung auszuwählen.
Weitere Fallstudien
Im Fall Nr. 1 (Abb. 1-2) schwankt der Luftbedarf stark zwischen Nacht- und Tagschicht, von etwa 30 m3/min bis 220 m3/min, was einer Variabilität von 90 Prozent des Durchflusses entspricht.
In Abb. 2 wird das Flussprofil in Fall Nr. 1 näher erläutert. Die y-Achse stellt den Anforderungsfluss als absolute Zahl auf der linken Seite und als Prozentsatz des maximalen angeforderten Systemflusses auf der rechten Seite dar. Die x-Achse zeigt die Zeit in Prozent des gesamten Beobachtungszeitraums. Aus diesen Daten kann der Forscher ableiten, dass die in Fall Nr. 1 dargestellte Anlage fast 50 % der Zeit unterhalb des durchschnittlichen Durchflusses arbeitet. Dieses Strömungsspektrum ist typisch für einen Produktionsstandort mit zwei sechsstündigen Nachtschichten mit geringem Luftbedarf und zwei sechsstündigen Tagesschichten mit hohem Luftbedarf.
Abb. 2: Durchflussspektrum mit hoher Variabilität (90 Prozent)
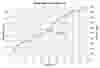
Die anderen vier analysierten Fälle sind in den Abbildungen 3 bis 6 dargestellt und sind repräsentativ für:
Fall Nr. 2 (Abb. 3): Ein weiteres hochvariables Spektrum mit 90 % Variabilität, aber im Vergleich zu Fall Nr. 1 wird nur in 30 % der Zeit weniger als der durchschnittliche Durchfluss angefordert. Dieses Spektrum ist typisch für eine Produktion mit einer achtstündigen Nachtschicht mit geringem Luftbedarf und zwei achtstündigen Tagesschichten mit hohem Luftbedarf.
Abb. 3: Flussprofil mit hoher Variabilität (90 Prozent) für mittlere Zeit
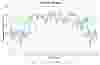
Fall Nr. 3 (Abb. 4): Ähnlich wie die Fälle Nr. 1 und Nr. 2, aber mit geringerer Variabilität als zuvor (ca. 65 Prozent des maximalen Durchflusses statt 90 Prozent). Zur Unterscheidung von den beiden vorangegangenen Fällen bezeichnen wir diesen Fall als einen Fall mit mittlerer Variabilität. Wie im Fall Nr. 1 tritt diese Schwankung über einen langen Zeitraum auf, da in etwa 50 % der Zeit weniger als der durchschnittliche Durchfluss angefordert wird.
Fall Nr. 4 (Abb. 5): Ein Flussmuster mit mittlerer Variabilität (ca. 65 Prozent des maximalen Flusses, wie in Fall Nr. 3); im Vergleich zu Fall Nr. 3 wird nur in 30 Prozent der Fälle weniger als der durchschnittliche Fluss angefordert.
Fall Nr. 5 (Abb. 6): Eine geringe Variabilität des Durchflusses mit einer Variabilität von nur etwa 30 Prozent des maximalen Durchflusses den ganzen Tag über, repräsentativ für 24 Stunden pro Tag - fast konstante Produktion.
ENERGIESPARENDE KOMPRESSORLÖSUNGEN
Unter dem Gesichtspunkt des Energieverbrauchs gibt es sechs alternative Kompressorlösungen für die in den Fällen 1-5 beschriebenen Situationen:
- Lösung A berücksichtigt einen Zentrifugalkompressor und einen großen (700 kW) Schraubenkompressor mit variabler Drehzahl, dessen maximaler Durchfluss die Hälfte des maximalen Durchflussbedarfs des Systems beträgt.
- Lösung B verwendet zwei Zentrifugalkompressoren, deren maximaler Durchfluss die Hälfte des maximalen Durchflussbedarfs des Systems beträgt. Es ist bekannt, dass Zentrifugalkompressoren für einen optimalen Wirkungsgrad mit einem kleineren Regelbereich oder einem großen Regelbereich, auch Turndown genannt, mit geringerem Wirkungsgrad ausgelegt werden können. Bei dieser zweiten Lösung sind die Kompressoren auf höchste Effizienz ausgelegt und verfügen über die neueste und effizienteste Lastverteilungsregelung.
- Solution C verwendet zwei Zentrifugalkompressoren, die für einen großen Regelbereich ausgelegt sind. Auch bei dieser Lösung, wie bei allen folgenden Lösungen mit mehreren Zentrifugalkompressoren, verfügen die Zentrifugalkompressoren über eine Lastverteilungsregelung, da dieses Regelsystem immer eine Reduzierung der Abblasemenge der Zentrifugalkompressoren ermöglicht, indem der Regelbereich des Systems erweitert wird.
- Lösung D berücksichtigt drei Zentrifugalkompressoren, deren maximaler Durchfluss ein Drittel des maximalen Durchflussbedarfs des Systems beträgt. Er ist für einen großen Regelbereich und eine Lastverteilung ausgelegt.
- Lösung E berücksichtigt gemischte Technologien, aber in diesem Fall gibt es zwei Zentrifugalkompressoren mit Lastverteilungsregelung und einen kleinen (160 kW) Schraubenkompressor mit variabler Drehzahl. In diesem Szenario werden die Kompressoren nicht durch einen Planer gesteuert. Das bedeutet, dass der kleine Schraubenkompressor mit variabler Drehzahl nur zur Deckung des Spitzenluftbedarfs eingesetzt wird.
- Lösung F verwendet die gleichen Kompressoren wie in E, aber in diesem Fall werden die drei Kompressoren von einem Planer gesteuert. Der Scheduler ermöglicht es dem System, jeden Kompressor nach einem vordefinierten Zeitplan zu betreiben - z. B. zu laden, zu entladen oder abzuschalten -, um das System unter verschiedenen Gesichtspunkten zu optimieren, in diesem Fall unter dem Gesichtspunkt des Energieverbrauchs.
Um auf unser ursprüngliches Strömungsprofil in Abb. 1 zurückzukommen: Lösung A - mit einem Zentrifugalverdichter und einem großen drehzahlgeregelten Rotationsverdichter - kann den vom System geforderten Durchfluss genau erfüllen. Aus diesem Grund ist es eine unschlagbare Kombination, denn es gibt keine verschwendete Luft. Wir müssen jedoch herausfinden, ob dies auch unter dem Gesichtspunkt des Energieverbrauchs die effizienteste Lösung ist. Die Verwendung eines einzigen Zentrifugalkompressors mit einem maximalen Volumenstrom, der dem maximalen Systembedarf entspricht, ist aufgrund der großen Menge an verschwendeter Luft keine praktikable Lösung, wie in Abb. 4 gezeigt. Aus diesem Grund wurde diese Konfiguration nicht in die Liste der zuvor diskutierten Lösungen aufgenommen.
Abb. 4: Luftabsaugung mit nur einem 220 m3/min Zentrifugalkompressor
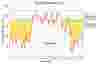
Wenn mehrere Zentrifugalkompressoren in einem System installiert sind, ist es möglich, das Abblasen der Zentrifugalkompressoren durch die Installation eines Lastverteilungsregelungssystems zu reduzieren. Die Abbildungen 8 und 9 zeigen den Unterschied im Regelbereich von zwei identischen Kompressoren, deren maximaler Volumenstrom die Hälfte des maximalen Luftbedarfs des Systems beträgt, ohne und mit Lastverteilungsregelung.
Abb. 5: Abblasen von Luft mit zwei 110 m3/min Zentrifugalkompressoren ohne Lastverteilungsregelung
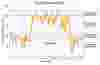
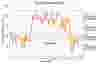
Bei variablem Förderstrombedarf, der über den natürlichen Regelbereich - auch Turn-Down" genannt - eines Radialverdichters hinausgeht, ist der Einsatz eines modernen Lastverteilungssystems immer dann von Vorteil, wenn zwei oder mehr Radialverdichter in einer Anlage eingesetzt werden, da das Abblasen der Luft reduziert wird.
Bei jeder der in den Lösungen B bis F beschriebenen Lösungen kann das System eine andere Menge an verbrauchter Luft aufweisen. In einigen Fällen, wie bei Lösung F (Abb. 7), ist das Abblasen der Luft minimal. Sie kommt dem Null-Abblasen in Lösung A sehr nahe, bei der ein Zentrifugalkompressor und ein großer Schraubenkompressor mit variabler Drehzahl verwendet werden. Dennoch ist es nicht die Minimierung des Luftablasses, die die besten Systeme bestimmt, sondern die Minimierung des Energieverbrauchs.
Abb. 7: Lösung F: Abblasen von Luft mit zwei 100 m3/min-Radialkompressoren, die auf Spitzenwirkungsgrad mit Lastverteilungsregelung ausgelegt sind, und einem drehzahlgeregelten Schraubenkompressor mit 25 m3/min (160 kW) mit Scheduler
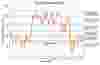
Betrachtet man die Leistungen bei einem Druck von 8 bar für jeden der in den Lösungen A bis F verwendeten Kompressoren, zeigt Abb. 8 den Vergleich des täglichen Energieverbrauchs für das Strömungsmuster von Fall Nr. 1 mit hoher Variabilität über einen langen Zeitraum. Sie zeigt auch die relative Effizienz zwischen Lösung A - der unschlagbaren Lösung - und den anderen fünf Lösungen. Der Wirkungsgrad von Lösung A wird als Referenz genommen und beträgt 100.
Abb. 8: Systemvergleich, täglicher Stromverbrauch
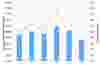
Lösung A ist nicht die unschlagbare Lösung, aber Lösung F - bestehend aus zwei Zentrifugalkompressoren mit Lastverteilung und einem kleinen 160-kW-Schraubenkompressor mit variabler Drehzahl und einem Scheduler - ist die beste Lösung in Bezug auf Energieeinsparung. Mit Lösung F kann der Nutzer im Vergleich zu Lösung A fast 3 % einsparen.
Lösung C - konfiguriert mit zwei Zentrifugalkompressoren, die für einen weiten Regelbereich und eine Lastverteilungssteuerung ausgelegt sind - weist trotz eines gewissen Luftablasses einen nur 0,3 Prozent niedrigeren Wirkungsgrad als Lösung A auf; daher ist sie aus betrieblicher Sicht die bessere Option. Wenn wir von 300 Betriebstagen pro Jahr und durchschnittlichen Energiekosten von 0,10 €/kWh (0,13 $/kWh) ausgehen, können die Betreiber mit Lösung A im Vergleich zu Lösung C nur 1500 € (19.500 $) pro Jahr sparen: Bei Lösung A werden zwei Kompressoren mit völlig unterschiedlichen Ersatzteilen verwendet, und wenn ein Reservekompressor benötigt wird, kann nur einer gewählt werden, was nicht die gleiche Betriebseffizienz garantiert. Lösung C, die zwei identische Zentrifugalkompressoren verwendet, beseitigt beide Probleme.
Abb. 9 zeigt den Vergleich der jährlichen reinen Energiekosten¹ der sechs Kompressorlösungen im Falle eines Luftstrommusters, wie in Fall Nr. 1. Eine weitere wichtige Überlegung ist die Bewertung des Verhaltens der sechs Lösungen für den Fall, dass zukünftige Produktionsänderungen den täglichen Luftverbrauch beeinflussen.
Abb. 9: Jährlicher Energiekostenvergleich in Fall Nr. 1.
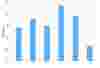
Die Strömungsmuster in den Fällen Nr. 2 bis 5 stellen verschiedene variable Luftstromprofile unter verschiedenen Produktionsbedingungen dar, die fast alle Lösungen abdecken - von den am stärksten variablen bis zu den am wenigsten variablen - wie in den Abbildungen 3 bis 6 dargestellt.
Tabelle 1 fasst die relativen Wirkungsgrade zwischen Lösung A und den anderen fünf Lösungen mit variablen Strömungsprofilen, wie in den Fällen Nr. 1 bis 5, zusammen.
Tabelle 1: Vergleich der Energieeffizienz: Die Effizienz von Lösung A wird als Referenz verwendet. Negative rote oder orangefarbene Prozentzahlen bedeuten, dass das System weniger effizient ist als Lösung A, und positive und grüne Zahlen bedeuten, dass das System effizienter ist als Lösung A. Gelb bedeutet, dass die beiden Systeme mehr oder weniger gleich sind. Die letzte Zeile zeigt die Rangfolge der sechs Lösungen unter Berücksichtigung der Effizienz des Systems (oder der jährlichen Energiekosten), der Flexibilität und der einfachen Bedienung, d. h. gemeinsame Ersatzteile und ein ebenso effizienter Ersatzkompressor.
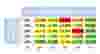
Betrachten wir nochmals die Kompressorleistung bei einem Druck von 8 bar, 300 Betriebstagen pro Jahr und durchschnittlichen Energiekosten von 0,10 €/kWh (0,13 $/kWh). Lösung F ermöglicht den Betreibern im Fall Nr. 1 Einsparungen von 15000 € (19.500 $) pro Jahr und im Fall Nr. 5 Einsparungen von etwa 40000 € (52.000 $) pro Jahr im Vergleich zu Lösung A. Lösung C hat etwas höhere Energiekosten, etwa 1500 € (1.950 $) pro Jahr im Fall Nr. 1, aber im Fall Nr. 5 ermöglicht sie Einsparungen von etwa 25000 € (32.500 $) pro Jahr im Vergleich zu Lösung A. 5 ermöglicht sie im Vergleich zu Lösung A Einsparungen von etwa 25000 € (32 500 $) pro Jahr. Bei der Bewertung von Fall Nr. 1 fragt man sich vielleicht, wie Lösung A - die in der Lage ist, genau den vom System geforderten Luftstrom ohne Abblasen der Luft zu liefern - fast den gleichen Wirkungsgrad hat wie Lösung C. Die Antwort ist in den Abbildungen 13 und 14 zu sehen.
Abb. 10 vergleicht die spezifische Leistung bei 8 bar verschiedener Zentrifugalmodelle mit großen Schraubenkompressoren mit variabler Drehzahl². Ein Zentrifugalkompressor mit 75 m3/min, der im Auslegungspunkt arbeitet, ist 19 % effizienter als ein 500-kW-Schraubenkompressor mit variabler Drehzahl; ein Zentrifugalkompressor mit 115 m3/min ist 14 % effizienter als ein 700-kW-Schraubenkompressor mit variabler Drehzahl; und ein Zentrifugalkompressor mit 140 m3/min ist 19 % effizienter als ein 900-kW-Schraubenkompressor mit variabler Drehzahl.
Abb. 10: Vergleich der spezifischen Paketleistung bei 8 bar
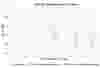
ÜBERLEGUNGEN ZU ZENTRIFUGALKOMPRESSOREN
Zusammenfassend lässt sich sagen, dass nur das Wissen um das tatsächliche Gewicht oder Gleichgewicht, in Form von Zeitanteilen oder variablen Betriebsbedingungen, es den Betreibern ermöglicht zu bestimmen, ob der große Schraubenkompressor mit variabler Drehzahl für das System geeignet ist. Dies ist ein wichtiges Konzept, das oft vernachlässigt oder missverstanden wird. Zur Verdeutlichung dieses Konzepts werden wir einen anderen realen Fall heranziehen.
Es gab einen Kunden mit fünf alten 4-Barren-Radialkompressoren verschiedener Größen von 70 m3/min bis 120 m3/min. Letztes Jahr beschloss er, den Kompressorraum zu modernisieren, um die Betriebskosten zu senken. Er sagte, dass ein Audit durchgeführt wurde und der erste Schritt darin bestand, die Effizienz des Systems zu verbessern. Um dies zu erreichen, beschloss er, einen Zentrifugalkompressor durch einen 500-kW-Schraubenkompressor mit variabler Drehzahl zu ersetzen.
Nach weiteren Untersuchungen stellten sie fest, dass der Hersteller an manchen Morgen zwischen 8 und 10 Uhr eine Produktionslinie abschalten musste, um sich auf die Glasart vorzubereiten, die am nächsten Tag hergestellt werden sollte. Während dieser zwei Stunden hatten sie einen Luftüberschuss von 60 m3/min. Da der alte Zentrifugalkompressor nur 20 m3/min regeln konnte, blies der Zentrifugalkompressor 40 m3/min an Luft ab. Durch den Austausch dieses Kompressors gegen einen 500-kW-Schraubenkompressor mit variabler Drehzahl hätte man jegliches Abblasen vermeiden und so die Effizienz des Systems verbessern und die Betriebskosten senken können.
Leider war dies ein falscher und irreführender Ansatz. Es stimmt zwar, dass ein 500-kW-Schraubenkompressor mit variabler Drehzahl ein Abblasen während der Stillstandszeit der Anlage verhindern würde, aber der Kunde hat einen realen Leistungsvergleich, wie in Abb. 12 dargestellt, nicht in Betracht gezogen. Der Kunde sollte einen Energiekostenvergleich zwischen einem neuen, zweistufigen Zentrifugalkompressor und dem gewünschten zweistufigen 500-kW-Schraubenkompressor mit variabler Drehzahl durchgeführt haben.
Abb. 12: Vergleich der spezifischen Paketleistung im Regelbereich bei 4 bar
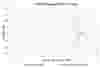
Aus den Datenblättern der Kompressoren geht hervor, dass ein 500-kW-Schraubenkompressor mit variabler Drehzahl bei einem Betriebsdruck von 4 bar einen um 43 % geringeren Wirkungsgrad hat als ein entsprechender Zentrifugalkompressor. Selbst wenn der Zentrifugalkompressor 13 m3/min ausbläst, ist er effizienter als der Schraubenkompressor mit variabler Drehzahl.
Um die beste Maschine für die Anwendung zu finden, hätte der Kunde die Kosten für das Abblasen von 40 m3/min für zwei Stunden pro Tag bewerten und die zusätzlichen Kosten für den Einsatz eines Kompressors mit einem um 43 % geringeren Wirkungsgrad für die restlichen 22 Stunden des Tages berechnen müssen.
Die Berechnungen zeigen:
Kosten des Abblasens:
40 m3/min × 4,3 kW/m3/min × 2 h/d × 350 d/y × 0,10 € ($0,13)/kWh ≈ 12.000 € ($15.600)/Jahr
Mehrkosten für die Verdichtung von 80 m3/min für 22 Stunden/Tag mit einem 43% weniger effizienten Kompressor:
80 m3/min × (6.0 - 4.2) kW/m3/min × 22 h/d × 350 d/y × 0.10 € ($0.13)/kWh ≈ 110.000 € ($144,000)/Jahr³
Um die Verschwendung von 12.000 € ($15.600)/Jahr aufgrund des Abblasens während der geplanten Stillstandszeit zu vermeiden, hätte der Kunde 110.000 € ($144.000)/Jahr mehr ausgegeben und für den Rest des Tages einen um 43 % weniger effizienten Kompressor betrieben. Selbst wenn man bedenkt, dass der drehzahlgeregelte Schraubenkompressor 22 Stunden pro Tag nicht immer unter Volllast arbeitet, ist der Unterschied so groß, dass man kaum behaupten kann, dass der Kunde durch den Kauf eines 500-kW-Schraubenkompressors anstelle eines neuen Zentrifugalkompressors Energie und Geld gespart hätte.
SCHLUSSFOLGERUNGEN
Die in diesem Artikel analysierten Fälle zeigen, dass der Einsatz von großen Schraubenkompressoren mit variabler Drehzahl (300-400 kW und mehr) selten die magische Lösung darstellt, die von einigen Kompressorherstellern oft behauptet wird, wenn ein Druckluftsystem große Luftmengen benötigt (ca. >100 m3/min) und der Luftbedarf während des Tages stark schwankt. Alternative Technologien oder Lösungen, wie der Zentrifugalkompressor mit Lastverteilungssteuerung, ermöglichen den Betreibern oft eine viel größere Energieeinsparung, trotz des Abblasens der Systemluft.
Tatsächlich können Zentrifugalkompressoren effizienter sein als große Schraubenkompressoren mit variabler Drehzahl, selbst wenn sie 10-15 % ihrer Nennleistung abblasen. Anstatt zu prüfen, ob eine Kompressortechnologie das Abblasen von Druckluft reduziert, wird empfohlen, den Wirkungsgrad des Kompressors über seinen Betriebsbereich, d. h. bei Voll- und Teillast, zu bewerten.
Erstens ist es wichtig, das genaue Strömungsprofil und das Strömungsspektrum des Systems zu kennen, um zu bestimmen, wie lange der Kompressor in einem Zustand arbeitet und wie lange in einem anderen, z. B. beim Abblasen von Luft oder beim Betrieb nahe seiner Auslegungsleistung. Aus diesem Grund ist es wichtig, vor Beginn einer Bewertung eine Luftanalyse durchzuführen. Die Ergebnisse müssen richtig gelesen und interpretiert werden - und dürfen nicht dazu benutzt werden, den Verkauf eines Kompressors zu rechtfertigen!
Dennoch ist jeder Fall kundenspezifisch, und mehrere Aspekte, die die endgültige Wahl beeinflussen könnten, sollten berücksichtigt werden: Installationsanforderungen, Platzbedarf, Bedarf an Backup-Einheiten und/oder Ersatzteillager, Flexibilität des Systems im Falle unterschiedlicher zukünftiger Produktionsanforderungen und anfängliche Kapitalinvestitionen. Die Anfangsinvestitionen wurden in dieser Studie bewusst nicht berücksichtigt, da die Systeme nur unter dem Gesichtspunkt des Energieverbrauchs bewertet werden sollten. Die Anfangsinvestition und die Amortisationsdauer würden die endgültige Entscheidung bestimmen. Ohne auf Preisdiskussionen oder Details einzugehen, dürften die Lösungen B und C die geringsten Anfangsinvestitionen aufweisen.