Optimizar un sistema de aire comprimido con una demanda de aire muy fluctuante
Resumen
Cuando un sistema de aire requiere grandes cantidades de aire (aprox. >100 m3/min) y la demanda de aire fluctúa mucho durante el día, los usuarios finales suelen creer que los grandes compresores de tornillo de velocidad variable pueden ofrecer importantes oportunidades de ahorro al adaptar con precisión el caudal de aire comprimido a la demanda del sistema.
Consideremos como ejemplo el caso representado en la Fig. 1. Cuando la demanda diaria de caudal tiene una variabilidad de hasta el 90% de la demanda máxima de aire, el estudio compara el consumo energético de seis soluciones alternativas en términos de número de compresores instalados, tamaños de los compresores y tipos de tecnologías de compresión (es decir, centrífuga exenta de aceite y rotativa exenta de aceite).
Fig. 1: Perfil de caudal de alta variabilidad (90%) para un periodo de 24 horas.
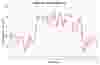
En el análisis también se tiene en cuenta la influencia del sistema de control de un compresor de aire y sus diferentes lógicas de control.
A continuación, se compara el consumo energético de las mismas seis soluciones con distintos patrones de demanda de aire para simular el comportamiento de los seis sistemas en caso de que varíen las necesidades de producción (es decir, también se consideran otros cuatro patrones diarios de demanda de aire con distinta variabilidad).
SELECCIONAR LA SOLUCIÓN DE AIRE COMPRIMIDO ADECUADA
Existen diferentes tecnologías de compresión y cada una puede tener sus propias ventajas e inconvenientes, en función de la aplicación concreta, el rango de funcionamiento, la potencia, la capacidad y otros aspectos.
Sin embargo, cuando un sistema de aire requiere grandes cantidades de aire y la demanda fluctúa mucho a lo largo del día, es común entre los usuarios finales la creencia de que sólo el uso de grandes compresores de tornillo de velocidad variable puede ofrecer grandes oportunidades de ahorro al adaptar exactamente el caudal de aire comprimido suministrado a la demanda de un sistema.
El objetivo de este estudio es comparar y evaluar seis soluciones diferentes de aire comprimido cuando la demanda de aire es muy fluctuante. El estudio consideró cinco perfiles de caudal variable, como se representa en las figuras 1 a 5, para definir algunas directrices que ayuden a los usuarios finales a seleccionar el mejor sistema para su aplicación.
CASOS PRÁCTICOS RELACIONADOS
En el caso nº 1 (Fig. 1-2), la demanda de aire fluctúa mucho entre los turnos de noche y de día, de aproximadamente 30 m3/min a 220 m3/min, lo que representa una variabilidad del 90% del caudal.
La Fig. 2 define con más detalle el perfil de flujo en el caso nº 1. El eje y representa el caudal solicitado como cifra absoluta a la izquierda, y como porcentaje del caudal máximo solicitado del sistema a la derecha. El eje x muestra el tiempo como porcentaje del periodo total de observación. A la vista de estos datos, el investigador puede deducir que la planta representada en el caso nº 1 funciona por debajo del caudal medio casi el 50% del tiempo. Este espectro de flujo es típico de un centro de producción con dos turnos nocturnos de seis horas con baja demanda de aire y dos turnos diurnos de seis horas con alta demanda de aire.
Fig. 2: Espectro de flujo de alta variabilidad (90%)
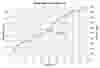
Los otros cuatro casos analizados se muestran en las figuras 3 a 6 y son representativos de:
Caso nº 2 (Fig. 3): Otro espectro muy variable con un 90% de variabilidad, pero en comparación con el Caso nº 1, sólo se solicita menos caudal que la media el 30% de las veces. Este espectro es típico de una producción con un turno nocturno de ocho horas con baja demanda de aire y dos turnos diurnos de ocho horas con alta demanda de aire.
Fig. 3: Perfil de flujo de alta variabilidad (90%) para tiempo medio
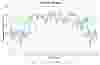
Caso nº 3 (Fig. 4): Similar a los casos nº 1 y nº 2 pero con menor variabilidad que antes (aprox. 65% del caudal máximo en lugar de 90%). Para diferenciarlo de los dos casos anteriores, lo denominamos caso de variabilidad media. En cuanto al caso nº 1, esta variabilidad se produce durante mucho tiempo, ya que se solicita un caudal inferior a la media durante aproximadamente el 50% del tiempo.
Caso nº 4 (Fig. 5): Un modelo de caudal de variabilidad media (aproximadamente el 65% del caudal máximo, como en el caso nº 3); en comparación con el caso nº 3, sólo se solicita un caudal inferior a la media el 30% de las veces.
Caso nº 5 (Fig. 6): Un patrón de flujo de baja variabilidad con una variabilidad de sólo aproximadamente el 30 por ciento del flujo máximo durante todo el día, representativo de 24 horas al día - producción casi constante.
SOLUCIONES DE AHORRO ENERGÉTICO PARA COMPRESORES
Desde el punto de vista del consumo de energía, existen seis soluciones alternativas de compresores para las situaciones descritas en los casos 1-5:
- Solución A considera un compresor centrífugo y un compresor de tornillo grande (700 kW) de velocidad variable cuyo caudal máximo es la mitad de la demanda de caudal máximo del sistema.
- Solución B utiliza dos compresores centrífugos cuyo caudal máximo es la mitad de la demanda máxima de caudal del sistema. Se sabe que los compresores centrífugos pueden diseñarse para obtener la máxima eficiencia con un rango de regulación menor o un rango de regulación amplio, también llamado turndown, con una eficiencia de diseño menor. En esta segunda solución, los compresores están diseñados para alcanzar la máxima eficiencia y cuentan con el control de carga compartida más moderno y eficaz.
- Solution C utiliza dos compresores centrífugos diseñados con un amplio rango de regulación. También en esta solución, como en todas las siguientes con múltiples compresores centrífugos, los compresores centrífugos tienen un control de carga compartida, ya que este sistema de control siempre permite reducir el soplado de los compresores centrífugos ampliando el rango de regulación del sistema.
- Solución D considera tres compresores centrífugos cuyo caudal máximo es un tercio de la demanda de caudal máximo del sistema. Está diseñado para una amplia reducción y control de carga compartida.
- La solución E contempla tecnologías mixtas, pero en este caso hay dos compresores centrífugos con control de carga compartida y un pequeño compresor de tornillo de velocidad variable (160 kW). En este escenario, los compresores no están controlados por un planificador. Esto significa que el pequeño compresor de tornillo de velocidad variable sólo se utiliza para cubrir los picos de demanda de aire.
- Solución F utiliza los mismos compresores que en E, pero en este caso los tres compresores están controlados por un programador. El programador permite que el sistema haga funcionar -por ejemplo, para cargar, descargar o apagar- cada compresor según un programa predefinido con el fin de optimizar el sistema desde varios puntos de vista; en este caso, desde el punto de vista del consumo de energía.
Volviendo a nuestro perfil de caudal original de la Fig. 1, la solución A -con un compresor centrífugo y un gran compresor rotativo de velocidad variable- puede ajustarse exactamente al caudal solicitado por el sistema. Por este motivo, es una combinación inmejorable, ya que no se desperdicia aire. Sin embargo, lo que tenemos que establecer es si también es la solución más eficiente desde el punto de vista del consumo de energía. El uso de un único compresor centrífugo con un caudal máximo igual a la demanda máxima del sistema no es una solución viable debido a la gran cantidad de aire desperdiciado, como se muestra en la Fig. 4. Por este motivo, esta configuración no se incluyó entre las soluciones analizadas anteriormente.
Fig. 4: Soplado de aire con un solo compresor centrífugo de 220 m3/min
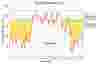
Cuando se instalan varios compresores centrífugos en un sistema, es posible reducir el soplado de los compresores centrífugos con la instalación de un sistema de control de carga compartida. Las Figs. 8 y 9 muestran la diferencia, en términos de rango de regulación de dos compresores idénticos, cuyo caudal máximo es la mitad de la demanda máxima de aire del sistema, sin y con un sistema de control de carga compartida.
Fig. 5: Soplado de aire con dos compresores centrífugos de 110 m3/min sin control de carga compartida
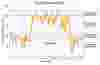
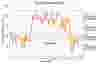
En caso de demanda de caudal variable más allá del rango de regulación natural -también llamado "turn-down"- de un compresor centrífugo, el uso de un sistema de control de carga compartida de última generación siempre es beneficioso cuando se utilizan dos o más compresores centrífugos en un sistema, ya que se reduce el soplado de aire.
Cada una de las soluciones descritas en las Soluciones B a F permite que el sistema tenga una cantidad diferente de aire desperdiciado. En algunos casos, como la solución F (Fig. 7), el soplado de aire es mínimo. Se aproxima mucho al soplado cero de la solución A, que utiliza un compresor centrífugo y un compresor de tornillo grande de velocidad variable. Sin embargo, no es la minimización del soplado de aire lo que determina los mejores sistemas, sino la minimización del consumo de energía.
Fig. 7: En la solución F, soplado de aire con dos compresores centrífugos de 100 m3/min diseñados para alcanzar la máxima eficiencia con control de carga compartida más un compresor de tornillo de velocidad variable de 25 m3/min (160 kW) con programador
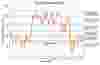
Considerando los rendimientos a una presión de 8 barg para cada uno de los compresores utilizados en las Soluciones A a F, la Fig. 8 muestra la comparación del consumo diario de energía para el patrón de flujo del Caso nº 1 con alta variabilidad durante un tiempo prolongado. También muestra la eficacia relativa entre la solución A -la solución imbatible- y las otras cinco soluciones. La eficacia de la solución A se toma como referencia y es igual a 100.
Fig. 8: Comparación de sistemas, consumo energético diario
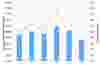
La solución A no es imbatible, pero la solución F -compuesta por dos compresores centrífugos con reparto de carga y un pequeño compresor de tornillo de velocidad variable de 160 kW con programador- es la mejor en términos de ahorro energético. La solución F permite al usuario ahorrar casi un 3% en comparación con la solución A.
La solución C -configurada con dos compresores centrífugos diseñados con un amplio rango de regulación y control de carga compartida-, a pesar de algunas purgas de aire, sólo es un 0,3% menos eficiente que la solución A; por lo tanto, es una opción preferible desde el punto de vista operativo. De hecho, si consideramos 300 días de funcionamiento al año y un coste energético medio de 0,10 €/kWh (0,13 $/kWh), la solución A permite a los operadores ahorrar sólo 1.500 € (19.500 $) al año frente a la solución C. Este ahorro no justifica las desventajas de funcionamiento de este sistema: La solución A utiliza dos compresores con piezas de repuesto completamente distintas y, si se necesita un compresor de reserva, sólo se puede elegir uno, lo que no garantiza la misma eficacia de funcionamiento. La solución C, que utiliza dos compresores centrífugos idénticos, elimina ambos problemas.
La Fig. 9 muestra la comparación de los costes anuales de energía pura¹ de las seis soluciones de compresores en caso de un patrón de flujo de aire, según el Caso nº 1. Otra consideración importante es evaluar el comportamiento de las seis soluciones en caso de que futuros cambios en la producción afecten al consumo diario de aire.
Fig. 9: Comparación de los costes energéticos anuales en el caso nº 1.
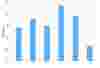
Los patrones de flujo de los casos n.º 2 a 5 representan diferentes perfiles de flujo de aire variable en diversas condiciones de producción, que abarcan casi todas las soluciones -desde la más variable a la menos variable-, como se representa en las Figs. 3 a 6.
La tabla 1 resume las eficiencias relativas entre la solución A y las otras cinco soluciones con perfiles de caudal variables, como en los casos nº 1 a 5.
Tabla 1: Comparación de la eficiencia energética: La eficiencia de la solución A se utiliza como referencia. Los porcentajes rojos o naranjas negativos indican que el sistema es menos eficiente que la solución A, y los positivos y verdes, que el sistema es más eficiente que la solución A. El amarillo significa que los dos sistemas son más o menos iguales. La última fila muestra la clasificación de las seis soluciones teniendo en cuenta la eficiencia del sistema (o los costes energéticos anuales), la flexibilidad y la facilidad de funcionamiento, es decir, piezas de repuesto comunes y un compresor de reserva igual de eficiente.
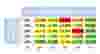
Consideremos de nuevo el rendimiento de un compresor a una presión de 8 barg, 300 días de funcionamiento al año y un coste energético medio de 0,10 €/kWh (0,13 $/kWh). La Solución F permite a los operadores ahorrar 15000 € (19.500 $) al año en el Caso nº 1 y aproximadamente 40000 € (52.000 $) al año en el Caso nº 5, en comparación con la Solución A. La Solución C tiene unos costes energéticos ligeramente superiores, unos 1500 € (1.950 $) al año en el Caso nº 1, pero en el Caso nº . 5 permite ahorrar aproximadamente 25.000 euros (32.500 dólares) al año en comparación con la solución A. Al evaluar el caso nº 1, uno puede preguntarse cómo es posible que la solución A, capaz de suministrar exactamente el caudal de aire solicitado por el sistema sin ninguna purga de aire, tenga casi la misma eficacia que la solución C. La respuesta se revela en las Figs. 13 y 14.
La Fig. 10 compara la potencia específica a 8 barg de diferentes modelos centrífugos con grandes compresores de tornillo de velocidad variable². Un compresor centrífugo de 75 m3/min trabajando en el punto de diseño es un 19% más eficiente que un compresor de tornillo de velocidad variable de 500 kW; un compresor centrífugo de 115 m3/min es un 14% más eficiente que un compresor de tornillo de velocidad variable de 700 kW; y un compresor centrífugo de 140 m3/min es un 19% más eficiente que un compresor de tornillo de velocidad variable de 900 kW.
Fig. 10: Comparación de la potencia específica del paquete a 8 barg
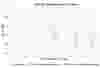
CONSIDERACIONES PARA COMPRESORES CENTRÍFUGOS
En resumen, sólo el conocimiento del peso o balance real, en términos de porcentaje de tiempo o condiciones variables de funcionamiento, permite a los operadores determinar si el compresor de aire de tornillo de velocidad variable grande es el adecuado para el sistema. Se trata de un concepto importante que a menudo se descuida o se malinterpreta. Utilizaremos otro caso real para aclarar este concepto.
Había un cliente con cinco viejos compresores centrífugos de 4 barg de distintos tamaños que oscilaban entre 70 m3/min y 120 m3/min. El año pasado decidió actualizar la sala de compresores para reducir los costes operativos. Dijo que se había realizado una auditoría y que el primer paso era mejorar la eficiencia de su sistema. Para ello, decidió sustituir un compresor centrífugo por un compresor de tornillo de velocidad variable de 500 kW.
Tras investigar más a fondo, determinaron que algunas mañanas, entre las 8 y las 10 de la mañana, el fabricante tenía que parar una línea de producción para preparar el tipo de vidrio que se iba a producir al día siguiente. Durante esas dos horas, tuvieron un exceso de aire de 60 m3/min. Como el antiguo compresor centrífugo sólo podía regular 20 m3/min, el compresor centrífugo expulsaba 40 m3/min de aire. Sustituyendo este compresor por un compresor de tornillo de velocidad variable de 500 kW, dijo, habrían podido evitar cualquier purga, mejorando la eficiencia del sistema y reduciendo los costes de explotación.
Desgraciadamente, se trataba de un planteamiento incorrecto y engañoso. Es cierto que un compresor de tornillo de velocidad variable de 500 kW evitaría el soplado durante el tiempo de inactividad de la planta, pero el cliente no tuvo en cuenta una comparación real del rendimiento, como se muestra en la Fig. 12. El cliente debería haber realizado una comparación de costes energéticos entre un compresor centrífugo de dos etapas nuevo y el compresor de tornillo de velocidad variable de 500 kW de dos etapas deseado.
Fig. 12: Comparación de la potencia específica del paquete en el rango de regulación a 4 barg
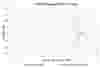
De las fichas técnicas de los compresores se deduce que, a una presión de funcionamiento de 4 barg, un compresor de tornillo de velocidad variable de 500 kW es un 43% menos eficiente que un compresor centrífugo equivalente. Aunque el compresor centrífugo expulse 13 m3/min, es más eficiente que el compresor de tornillo de velocidad variable.
Para determinar la mejor máquina para la aplicación, el cliente debería haber evaluado el coste de soplar 40 m3/min durante dos horas al día y haber calculado el sobrecoste de utilizar un compresor un 43% menos eficiente las 22 horas restantes del día.
Los cálculos revelan:
Coste del soplado:
40 m3/min × 4,3 kW/m3/min × 2 h/d × 350 d/a × 0,10 € (0,13 $)/kWh ≈ 12.000 € (15.600 $)/año
Coste extra por comprimir 80 m3/min durante 22 horas/día con un compresor un 43% menos eficiente:
80 m3/min × (6.0 - 4,2) kW/m3/min × 22 h/d × 350 d/a × 0,10 € (0,13 $)/kWh ≈ 110.000 € (144.000 $)/año³
Para evitar el derroche de 12.000 euros (15.600 dólares)/año debido a la descarga durante el tiempo de inactividad programado, el cliente habría gastado 110.000 euros (144.000 dólares)/año más, haciendo funcionar un compresor un 43% menos eficiente durante el resto del día. Incluso si tenemos en cuenta que 22 horas al día el compresor de tornillo de velocidad variable no siempre funciona a plena carga, la diferencia es tan grande que sería difícil afirmar que el cliente habría ahorrado energía y dinero comprando un compresor de tornillo de velocidad variable de 500 kW en lugar de un compresor centrífugo nuevo.
CONCLUSIONES
Los casos analizados en este artículo demuestran que cuando un sistema de aire requiere grandes cantidades de aire (aprox. >100 m3/min) y la demanda de aire fluctúa mucho durante el día, el uso de grandes compresores de tornillo de velocidad variable (300-400 kW y superiores) rara vez representa la solución mágica que suelen proclamar algunos fabricantes de compresores. Las tecnologías o soluciones alternativas, como el compresor centrífugo con control de carga compartida, a menudo permiten a los operadores obtener ahorros de energía mucho mayores, a pesar del soplado de aire del sistema.
De hecho, los compresores centrífugos pueden ser más eficientes que los grandes compresores de tornillo de velocidad variable aunque soplen un 10-15% de su capacidad de diseño. En lugar de evaluar si una tecnología de compresores reduce el soplado de aire comprimido, se recomienda que los operadores evalúen la eficiencia del compresor en su rango de funcionamiento, es decir, a plena carga y a cargas parciales.
En primer lugar, es importante conocer el perfil exacto de caudal y el espectro de caudal del sistema para determinar cuánto tiempo funcionará el compresor en una condición frente a otra, por ejemplo, soplando algo de aire frente a funcionando cerca de su capacidad de diseño. Por esta razón, es importante realizar una evaluación del aire antes de iniciar cualquier evaluación. Los resultados deben leerse e interpretarse correctamente, y no aprovecharse para justificar la venta de un compresor
No obstante, cada caso es específico del cliente y deben tenerse en cuenta varios aspectos que podrían influir en la elección final: requisitos de instalación, espacio en planta, necesidad de unidades de reserva y/o existencias de piezas de repuesto, flexibilidad del sistema en caso de diferentes necesidades de producción futuras e inversión de capital inicial. La inversión de capital inicial se excluyó intencionadamente de este estudio porque el objetivo era evaluar los sistemas únicamente desde el punto de vista del consumo de energía. La inversión de capital inicial y el periodo de amortización determinarán la decisión final. Sin entrar en discusiones sobre precios o detalles, es probable que las Soluciones B y C tengan las inversiones de capital iniciales más bajas.