- COMPONENTES Impulsores: Impulsores fresados en cinco ejes diseñados y fabricados con técnicas y métodos avanzados
- Difusores de paletas: Diseño y colocación de los álabes optimizados para aumentar la eficiencia
- Sistema de lubricación: Sistema de lubricación autónomo de baja presión
- Intercoolers/Aftercooler: El intercooler de agua en tubo y los paquetes de posenfriadores se deslizan hacia fuera para facilitar la inspección y la limpiezaDiseño avanzado de los cojinetes de piñón: Diseñado para una mayor vida útil y un funcionamiento con cualquier carga operativa.
- Juntas: Diseñado con sellos de aire y aceite de laberinto sin contacto y sin desgaste. No se requiere aire de amortiguación para el aire libre de aceite. No requieren una sustitución periódica como las juntas de anillo de carbono.
- Caja de engranajes inclinada horizontalmente: Permite un fácil acceso cuando la política de mantenimiento de la obra requiere una inspección periódica.
- Paletas guía de entrada variable: Los álabes guía de entrada variable pueden ofrecer un ahorro de energía de hasta el 9% cuando se opera en reducción. Los álabes guía de entrada imparten un movimiento de remolino al flujo de aire de entrada en la misma dirección que el funcionamiento del impulsor, reduciendo el trabajo de entrada. El ahorro neto de energía puede realizarse con un caudal reducido o en días más fríos que la temperatura de diseño. Los álabes guía de entrada se colocan cerca del inductor del impulsor para maximizar el rendimiento.
BAJO COSTO TOTAL DE PROPIEDAD
Con el tiempo, la energía necesaria para alimentar un sistema de aire comprimido es el mayor costo asociado a un compresor, especialmente en los fluctuantes mercados energéticos actuales. Por eso, para determinar con precisión la rentabilidad de su inversión, es importante tener en cuenta el costo total del ciclo de vida del compresor, incluyendo la inversión inicial, el consumo de energía y los costos de mantenimiento.
Como demuestra el gráfico de la derecha, el MSG TURBO-AIR 2000 ofrece uno de los costos totales del ciclo de vida más bajos de todos los compresores, incluidos los de tornillo seco, los de tornillo con accionamiento de velocidad variable (VSD) y otros compresores centrífugos.
En comparación con otras máquinas de capacidad similar, los compresores MSG TURBO-AIR 2000 son uno de los compresores exentos de aceite más eficientes a plena carga, a carga parcial y en vacío.
El ahorro de energía obtenido puede acelerar significativamente la recuperación de su inversión inicial, y el ahorro continúa aumentando cuanto más se utiliza el MSG TURBO-AIR 2000.
VENTAJAS DE LOS TURBOCOMPRESORES MSG
Aire libre de aceite con certificación ISO 8573-1
- Evita la contaminación por aceite de su sistema
- Limita el potencial de incendios en las tuberías de aire comprimido causados por el arrastre de aceite
- Elimina los costosos problemas de eliminación de residuos asociados a los condensados cargados de aceite
- Elimina el gasto y los requisitos de mantenimiento asociados a los filtros de eliminación de aceite, ya que no entra aceite en la corriente de aire comprimido del compresor
Instalación sencilla
- La capacidad de descarga real ayuda a aprovechar las oportunidades de ahorro de enerigia
- El mayor tiempo de funcionamiento en comparación con las tecnologías alternativas se traduce en una reducción de los costos del ciclo de vida operativa
- Menores conexiones externas
- El diseño compacto reduce el espacio necesario en el suelo Cumple los requisitos de nivel sonoro de la OSHA sin necesidad de un recinto acústico
Funcionamiento de bajo costo
- La verdadera capacidad de descarga ayuda a aprovechar las oportunidades de ahorro de energía
- El mayor tiempo de actividad en comparación con las tecnologías alternativas se traduce en una reducción de los costos del ciclo de vida operativo
- Excelentes eficiencias de carga parcial para cualquier carga de funcionamiento
- No hay piezas de deslizamiento o rozamiento en el proceso de compresión que causen desgaste o pérdida de eficiencia
Funcionamiento sencillo
- El panel de control MAESTRO™ Universal proporciona un servidor web integrado, lo que permite la supervisión del compresor mediante su intranet local
- Importante ahorro anual en el costo de funcionamiento al proporcionar un control más preciso
- Funcionamiento sencillo y automatico
Fácil mantenimiento
- Los elementos de compresión no se desgastan ni requieren una sustitución periódica
- No hay filtros de extracción de aceite que limpiar o sustituir
Fácil acceso horizontal a la caja de cambios dividida para una rapida inspección , - El paquete de intecooler y posenfriador son faciles de desmontar para su inspección y limpieza
- El intercooler y el posenfriador con diseño de agua en el tubo permiten una limpieza mecánica sencilla
- Acoplamiento en seco libre de mantenimiento
Alta fiabilidad
- Cargas de empuje absorbidas a baja velocidad
- Juntas de aire y aceite sin contacto
- Elementos de compresión de acero inoxidable
- Diseño de engranajes conservador y de alta calidad
- Diseño de cojinetes de piñón de larga duración
- Los compresores centrífugos han demostrado tener un largo tiempo medio entre fallos (MTBF), y una investigación independiente ha demostrado una disponibilidad líder en el sector del 99.7%
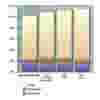