Otimize um Sistema de Ar Comprimido com Demanda de Ar Altamente Flutuante
Resumo
Quando um sistema de ar requer grandes quantidades de ar (aprox. >100 m3/min) e a demanda de ar flutua muito durante o dia, é comum os usuários finais acreditarem que os grandes compressores de parafuso de velocidade variável podem proporcionar oportunidades significativas de economia, combinando precisamente o fluxo de ar comprimido com a demanda do sistema.
Considere o caso descrito na Fig. 1 como um exemplo. Quando a demanda diária de fluxo tem uma variabilidade de até 90% da demanda máxima de ar, o estudo compara o consumo de energia de seis soluções alternativas em termos de número de compressores instalados, tamanhos de compressores e tipos de tecnologias de compressão (ou seja, centrífuga isenta de óleo e rotativa isenta de óleo).
Fig. 1: Perfil de fluxo de alta variabilidade (90%) para um período de 24 horas.
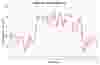
A influência do sistema de controle de um compressor de ar e suas diferentes lógicas de controle também é levada em consideração na análise.
O consumo de energia das mesmas seis soluções é então comparado com diferentes padrões de demanda de ar para simular o comportamento dos seis sistemas no caso de necessidades de produção variáveis (ou seja, outros quatro padrões diários de demanda de ar com variabilidade diferente também são considerados).
SELEÇÃO DA SOLUÇÃO DE AR COMPRIMIDO CORRETA
Existem diferentes tecnologias de compressão e cada uma delas pode ter suas próprias vantagens e desvantagens, dependendo da aplicação específica, da faixa de operação, da potência, da capacidade e de outros aspectos.
No entanto, quando um sistema de ar requer grandes quantidades de ar e a demanda de ar flutua muito durante o dia, é comum a crença entre os usuários finais de que somente o uso de grandes compressores de parafuso de velocidade variável pode proporcionar grandes oportunidades de economia, combinando exatamente o fluxo de ar comprimido fornecido com a demanda de um sistema.
O objetivo deste estudo é comparar e avaliar seis soluções diferentes de ar comprimido quando a demanda de ar é altamente flutuante. O estudo considerou cinco perfis de fluxo variável, conforme ilustrado nas Figuras 1 a 5, para definir algumas diretrizes para ajudar os usuários finais a selecionar o melhor sistema para sua aplicação.
CASOS DE ESTUDO RELACIONADOS
No Caso No. 1 (Fig. 1-2), a demanda de ar varia muito entre os turnos da noite e do dia, de aproximadamente 30 m3/min a 220 m3/min, o que representa uma variabilidade de 90% do fluxo.
A Fig. 2 define melhor o perfil de fluxo no Caso nº 1. O eixo y representa o fluxo de solicitação como um valor absoluto à esquerda e como uma porcentagem do fluxo máximo solicitado do sistema à direita. O eixo x mostra o tempo como uma porcentagem do período total de observação. Com base nesses dados, o pesquisador pode deduzir que a planta representada no Caso nº 1 opera abaixo do fluxo médio em quase 50% do tempo. Esse espectro de fluxo é típico de um local de produção com dois turnos noturnos de seis horas com baixa demanda de ar e dois turnos diurnos de seis horas com alta demanda de ar.
Fig. 2: Espectro de fluxo de alta variabilidade (90 por cento)
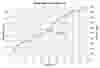
Os outros quatro casos analisados são mostrados nas Figuras 3 a 6 e são representativos:
Caso nº 2 (Fig. 3): Outro espectro altamente variável, com 90% de variabilidade, mas, em comparação com o Caso nº 1, um fluxo menor do que a média é solicitado em apenas 30% das vezes. Esse espectro é típico de uma produção com um turno noturno de oito horas com baixa demanda de ar e dois turnos diurnos de oito horas com alta demanda de ar.
Fig. 3: Perfil de fluxo de alta variabilidade (90%) para tempo médio
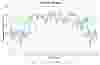
Caso nº 3 (Fig. 4): Semelhante aos casos nº 1 e nº 2, mas com menor variabilidade do que antes (cerca de 65% do fluxo máximo em vez de 90%). Para diferenciá-lo dos dois casos anteriores, chamamos esse caso de caso com variabilidade média. Quanto ao Caso nº 1, essa variabilidade ocorre por um longo período, já que um fluxo menor do que a média é solicitado em aproximadamente 50% do tempo.
Caso nº 4 (Fig. 5): Um padrão de fluxo de variabilidade média (cerca de 65% do fluxo máximo, como no Caso nº 3); em comparação com o Caso nº 3, um fluxo menor do que a média é solicitado somente em 30% das vezes.
Caso nº 5 (Fig. 6): Um padrão de fluxo de baixa variabilidade com uma variabilidade de apenas aproximadamente 30% do fluxo máximo durante todo o dia, representativo de 24 horas por dia - produção quase constante.
SOLUÇÕES DE COMPRESSORES COM ECONOMIA DE ENERGIA
Do ponto de vista do consumo de energia, há seis soluções alternativas de compressores para as situações descritas nos Casos 1-5:
- Solução A considera um compressor centrífugo e um compressor parafuso de velocidade variável grande (700 kW) cujo fluxo máximo é a metade da demanda de fluxo máximo do sistema.
- Solução B usa dois compressores centrífugos cuja vazão máxima é a metade da demanda máxima de vazão do sistema. Sabe-se que os compressores centrífugos podem ser projetados para obter a melhor eficiência com uma faixa de regulagem menor ou uma faixa de regulagem ampla, também chamada de turndown, com menor eficiência de projeto. Nessa segunda solução, os compressores são projetados para obter eficiência máxima e têm o controle de compartilhamento de carga mais recente e eficiente.
- A solução C utiliza dois compressores centrífugos projetados com ampla faixa de regulagem. Também nessa solução, como em todas as soluções a seguir com vários compressores centrífugos, os compressores centrífugos têm um controle de compartilhamento de carga, pois esse sistema de controle sempre permite a redução do blow-off dos compressores centrífugos, ampliando a faixa de regulagem do sistema.
- Solução D considera três compressores centrífugos cuja vazão máxima é um terço da demanda de vazão máxima do sistema. Ele foi projetado para uma ampla abertura e controle de compartilhamento de carga.
- A solução E considera tecnologias mistas, mas, nesse caso, há dois compressores centrífugos com controle de compartilhamento de carga e um pequeno compressor parafuso de velocidade variável (160 kW). Nesse cenário, os compressores não são controlados por um agendador. Isso significa que o pequeno compressor de parafuso de velocidade variável é usado apenas para atender às demandas de ar de pico.
- Solução F utiliza os mesmos compressores que em E, mas, nesse caso, os três compressores são controlados por um agendador. O programador permite que o sistema opere - por exemplo, para carregar, descarregar ou desligar - cada compressor de acordo com uma programação predefinida para otimizar o sistema de vários pontos de vista; nesse caso, do ponto de vista do consumo de energia.
Voltando ao nosso perfil de fluxo original na Fig. 1, a Solução A - com um compressor centrífugo e um grande compressor rotativo de velocidade variável - pode corresponder exatamente ao fluxo solicitado pelo sistema. Por esse motivo, é uma combinação imbatível, pois não há desperdício de ar. No entanto, o que precisamos estabelecer é se essa também é a solução mais eficiente do ponto de vista do consumo de energia. O uso de um único compressor centrífugo com um fluxo máximo igual à demanda máxima do sistema não é uma solução viável devido à grande quantidade de ar desperdiçado, conforme mostrado na Fig. 4. Por esse motivo, essa configuração não foi listada entre as soluções discutidas anteriormente.
Fig. 4: Sopro de ar com apenas um compressor centrífugo de 220 m3/min
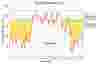
Quando vários compressores centrífugos são instalados em um sistema, é possível reduzir o blow-off dos compressores centrífugos com a instalação de um sistema de controle de compartilhamento de carga. As Figs. 8 e 9 mostram a diferença, em termos de faixa de regulagem, de dois compressores idênticos, cujo fluxo máximo é metade da demanda máxima de ar do sistema, sem e com um sistema de controle de compartilhamento de carga.
Fig. 5: Descarga de ar com dois compressores centrífugos de 110 m3/min sem controle de compartilhamento de carga
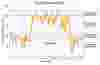
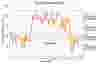
No caso de demanda de vazão variável além da faixa de regulagem natural - também chamada de "turn-down" - de um compressor centrífugo, o uso de um sistema de controle de compartilhamento de carga de última geração é sempre benéfico quando dois ou mais compressores centrífugos são usados em um sistema, uma vez que o sopro de ar é reduzido.
Cada uma das soluções descritas nas Soluções B a F permite que o sistema tenha uma quantidade diferente de ar desperdiçado. Em alguns casos, como na Solução F (Fig. 7), o sopro de ar é mínimo. É muito próximo do blow-off zero na Solução A, usando um compressor centrífugo e um grande compressor parafuso de velocidade variável. No entanto, não é a minimização do sopro de ar que determina os melhores sistemas, mas a minimização do consumo de energia.
Fig. 7: Na Solução F, sopro de ar com dois compressores centrífugos de 100 m3/min projetados para eficiência máxima com controle de compartilhamento de carga mais um compressor parafuso de velocidade variável de 25 m3/min (160 kW) com programador
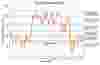
Considerando os desempenhos a uma pressão de 8 barg para cada um dos compressores usados nas Soluções A a F, a Fig. 8 mostra a comparação do consumo diário de energia para o padrão de fluxo do Caso nº 1 com alta variabilidade por um longo período. Ele também mostra a eficiência relativa entre a Solução A - a solução imbatível - e as outras cinco soluções. A eficiência da Solução A é considerada como referência e é igual a 100.
Fig. 8: Comparação de sistemas, consumo diário de energia
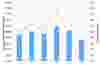
A solução A não é imbatível, mas a solução F - composta por dois compressores centrífugos com compartilhamento de carga e um pequeno compressor parafuso de velocidade variável de 160 kW com um programador - é a melhor solução em termos de conservação de energia. A solução F permite que o usuário economize quase 3% em comparação com a solução A.
A solução C - configurada com dois compressores centrífugos projetados com ampla faixa de regulagem e controle de compartilhamento de carga -, apesar de algum escape de ar, tem eficiência apenas 0,3% menor do que a solução A; portanto, é uma opção preferível do ponto de vista operacional. De fato, se considerarmos 300 dias de operação por ano e um custo médio de energia de 0,10 €/kWh (US$ 0,13/kWh), a Solução A permite que os operadores economizem apenas 1.500 € (US$ 19.500) por ano em relação à Solução C. Essa economia não justifica as desvantagens operacionais desse sistema: A solução A utiliza dois compressores com peças de reposição completamente diferentes e, se for necessário um compressor de reserva, apenas um pode ser escolhido, o que não garante a mesma eficiência operacional. A solução C, usando dois compressores centrífugos idênticos, elimina esses dois problemas.
A Fig. 9 mostra a comparação dos custos anuais de energia pura¹ das seis soluções de compressores no caso de um padrão de fluxo de ar, conforme o Caso nº 1. Outra consideração importante é avaliar o comportamento das seis soluções no caso de mudanças futuras na produção afetarem o consumo diário de ar.
Fig. 9: Comparação dos custos anuais de energia no Caso nº 1.
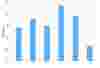
Os padrões de fluxo nos Casos nº 2 a 5 representam diferentes perfis de fluxo de ar variável em várias condições de produção, que abrangem quase todas as soluções - da mais variável à menos variável - conforme ilustrado nas Figs. 3 a 6.
A Tabela 1 resume as eficiências relativas entre a Solução A e as outras cinco soluções com perfis de fluxo variáveis, como nos Casos nº 1 a 5.
Tabela 1: Comparação da eficiência energética: A eficiência da Solução A é usada como referência. As porcentagens negativas em vermelho ou laranja indicam que o sistema é menos eficiente que a Solução A, e os números positivos e verdes indicam que o sistema é mais eficiente que a Solução A. Amarelo significa que os dois sistemas são mais ou menos iguais. A última linha mostra a classificação das seis soluções considerando a eficiência do sistema (ou custos anuais de energia), a flexibilidade e a facilidade de operação, ou seja, peças de reposição comuns e um compressor de reserva igualmente eficiente.
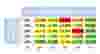
Considere novamente o desempenho do compressor em uma pressão de 8 barg, 300 dias de operação por ano e um custo médio de energia de 0,10 €/kWh (US$ 0,13/kWh). A Solução F permite que os operadores economizem 15000 € ($19500) por ano no Caso nº 1 e aproximadamente 40000 € ($52.000) por ano no Caso nº 5, em comparação com a Solução A. A Solução C tem custos de energia ligeiramente mais altos, cerca de 1500 € ($1950) por ano no Caso nº 1, mas no Caso nº 5, ela permite uma economia de aproximadamente 25000 euros (US$ 32.500) por ano em comparação com a Solução A. Avaliando o Caso nº 1, uma pessoa pode se perguntar como a Solução A - que é capaz de fornecer exatamente o fluxo de ar solicitado pelo sistema sem qualquer sopro de ar - tem quase a mesma eficiência que a Solução C. A resposta é revelada nas Figs. 13 e 14.
A Fig. 10 compara a potência específica a 8 barg de diferentes modelos centrífugos com grandes compressores de parafuso de velocidade variável². Um compressor centrífugo de 75 m3/min trabalhando no ponto de projeto é 19% mais eficiente do que um compressor parafuso de velocidade variável de 500 kW; um compressor centrífugo de 115 m3/min é 14% mais eficiente do que um compressor parafuso de velocidade variável de 700 kW; e um compressor centrífugo de 140 m3/min é 19% mais eficiente do que um compressor parafuso de velocidade variável de 900 kW.
Fig. 10: Comparação da potência específica do pacote a 8 barg
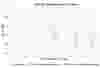
CONSIDERAÇÕES SOBRE COMPRESSORES CENTRÍFUGOS
Em resumo, somente o conhecimento do peso ou equilíbrio real, em termos de porcentagem de tempo ou condições operacionais variáveis, permite que os operadores determinem se o compressor de ar de parafuso de velocidade variável grande é adequado para o sistema. Esse é um conceito importante que muitas vezes é negligenciado ou mal compreendido. Usaremos outro caso real para esclarecer esse conceito.
Havia um cliente com cinco compressores centrífugos antigos de 4 barg de vários tamanhos, variando de 70 m3/min a 120 m3/min. No ano passado, ele decidiu atualizar a sala de compressores para reduzir os custos operacionais. Ele disse que foi realizada uma auditoria e a primeira etapa foi melhorar a eficiência do sistema. Para isso, ele decidiu substituir um compressor centrífugo por um compressor de ar de parafuso de velocidade variável de 500 kW.
Após uma investigação mais aprofundada, eles determinaram que, em algumas manhãs, entre as 8 e 10 horas, o fabricante tinha de fechar uma linha de produção para se preparar para o tipo de vidro a ser produzido no dia seguinte. Durante essas duas horas, eles tiveram um excesso de ar de 60 m3/min. Como o antigo compressor centrífugo era capaz de regular apenas 20 m3/min, o compressor centrífugo estava soprando 40 m3/min de ar. Ao substituir esse compressor por um compressor de parafuso de velocidade variável de 500 kW, ele disse que teria sido possível evitar qualquer sopro, melhorando a eficiência do sistema e reduzindo os custos operacionais.
Infelizmente, essa foi uma abordagem incorreta e enganosa. É verdade que um compressor de parafuso de velocidade variável de 500 kW evitaria o blow-off durante o tempo de inatividade da fábrica, mas o cliente não considerou uma comparação real de desempenho, conforme mostrado na Fig. 12. O cliente deveria ter realizado uma comparação de custo de energia entre um novo compressor centrífugo de dois estágios e o desejado compressor parafuso de dois estágios e velocidade variável de 500 kW.
Fig. 12: Comparação da potência específica do pacote na faixa de regulagem a 4 barg
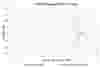
Pode-se deduzir das folhas de dados do compressor que, em uma pressão operacional de 4 barg, um compressor de parafuso de velocidade variável de 500 kW é 43% menos eficiente do que um compressor centrífugo equivalente. Mesmo que o compressor centrífugo esteja soprando 13 m3/min, ele é mais eficiente do que o compressor de parafuso de velocidade variável.
Para determinar a melhor máquina para a aplicação, o cliente deveria ter avaliado o custo de soprar 40 m3/min durante duas horas por dia e calculado o custo extra de usar um compressor 43% menos eficiente nas 22 horas restantes do dia.
Os cálculos revelam:
Custo do blow-off:
40 m3/min × 4,3 kW/m3/min × 2 h/d × 350 d/ano × 0,10 € (US$ 0,13)/kWh ≈ 12.000 € (US$ 15.600)/ano
Custo extra para comprimir 80 m3/min por 22 horas/dia com um compressor 43% menos eficiente:
80 m3/min × (6.0 - 4,2) kW/m3/min × 22 h/d × 350 d/ano × 0,10 € ($0,13)/kWh ≈ 110.000 € ($144.000)/ano³
Para evitar o desperdício de 12.000 € (US$ 15.600)/ano devido ao blow-off durante o tempo de inatividade programado, o cliente teria gasto 110.000 € (US$ 144.000)/ano a mais, operando um compressor 43% menos eficiente durante o resto do dia. Mesmo se considerarmos que 22 horas/dia o compressor de parafuso de velocidade variável nem sempre trabalha a plena carga, a diferença é tão grande que seria difícil afirmar que o cliente teria economizado energia e dinheiro comprando um compressor de parafuso de velocidade variável de 500 kW em vez de um novo compressor centrífugo.
CONCLUSÕES
Os casos analisados neste artigo mostram que, quando um sistema de ar requer grandes quantidades de ar (aprox. >100 m3/min) e a demanda de ar flutua muito durante o dia, o uso de grandes compressores de parafuso de velocidade variável (300-400 kW e acima) raramente representa a solução mágica que é frequentemente reivindicada por alguns fabricantes de compressores. Tecnologias ou soluções alternativas, como o compressor centrífugo com controle de compartilhamento de carga, muitas vezes permitem que os operadores obtenham uma economia de energia muito maior, apesar da descarga de ar do sistema.
De fato, os compressores centrífugos podem ser mais eficientes do que os grandes compressores de parafuso de velocidade variável, mesmo que eles queimem de 10 a 15% de sua capacidade projetada. Em vez de avaliar se uma tecnologia de compressor reduz o sopro de ar comprimido, recomenda-se que os operadores avaliem a eficiência do compressor em sua faixa de operação, ou seja, em carga total e cargas parciais.
Primeiro, é importante conhecer o perfil exato do fluxo do sistema e o espectro de fluxo para determinar quanto tempo o compressor operará em uma condição versus outra, por exemplo, soprando um pouco de ar versus operando próximo à sua capacidade de projeto. Por esse motivo, é importante realizar uma avaliação do ar antes de iniciar qualquer avaliação. Os resultados devem ser lidos e interpretados corretamente, e não explorados para justificar a venda de um compressor!
No entanto, cada caso é específico do cliente e vários aspectos que podem influenciar a escolha final devem ser considerados: requisitos de instalação, espaço físico, necessidade de unidades de backup e/ou estoque de peças sobressalentes, flexibilidade do sistema em caso de diferentes necessidades futuras de produção e investimento de capital inicial. O investimento de capital inicial foi intencionalmente excluído deste estudo porque o escopo era avaliar os sistemas apenas do ponto de vista do consumo de energia. O investimento de capital inicial e o período de retorno do investimento determinariam a decisão final. Sem entrar em discussões ou detalhes sobre preços, é provável que as soluções B e C tenham os investimentos de capital iniciais mais baixos.