Global Trends in the Electric Vehicle Battery Market
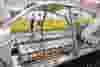
The supply chain for EV batteries is fairly simple, with the basic components of the cycle including:
Upstream: the process of mining the raw materials that go into creating the batteries, e.g., lithium, nickel, etc.
Midstream: these raw materials are then processed and refined, purifying them to enable the creation of cathode and anode battery materials, which are then sold on to firms that produce battery cells
Downstream: these are the battery manufacturers, the ones who turn these materials into the final product in order to place them into electric vehicles
End of Life: when these batteries no longer work or serve their purpose, they can either be reused or recycled
Reused or Recycled: life for these EV batteries doesn't end there; they can then be either reused or recycled, further contributing to a sustainable future
You might be wondering what role compressed air plays in this process. In reality, your EV battery manufacturing plant can't actually live without it! In the electrode production, battery cell assembly, and cell finishing of EV battery manufacturing, high-quality compressed air is essential for a range of different applications. Without it, your machinery will be unable to carry out all of these crucial processes. Therefore, it’s essential to have a range of critical process solutions, including air compressors, nitrogen generators, vacuum, pumping and lifting technologies, all in place to guarantee optimum efficiency! That’s where we come in!
So, Let’s Take a Look at Our Vacuum Solutions & Why They Are So Important For EV Battery Manufacturing…
The Ingersoll Rand portfolio of brands, including Nash Vacuum Pumps, provide dry running claw and dry screw vacuum solutions ideal for EV battery manufacturing processes, including for electrode coating, cell assembly, and finishing or packaging.
Some common subprocesses leveraging dry vacuum technologies include electrode (anode and/or cathode) drying and filling and formation for electrode coating, and vacuum heat drying and vacuum filling during the cell assembly process, and degassing for Cell Finishing and Packaging.
Ingersoll Rand’s Nash vacuum pumps include a broad choice of technologies, including claw dry running vacuum pumps and systems as well as market-leading dry screw technologies.
We also offer a range of pumping solutions, which play an integral role in EV battery manufacturing…
Chemical metering pumps and mixing equipment are used at every stage of the lithium-ion battery process, from the initial extraction of precious metals in the mining process through to battery precursors and chemical production to final assembly and recycling. The use of harsh chemicals, such as adhesives, solvents, and the transferring of slurries, powders, solids, and viscous fluids in multiple steps throughout the manufacturing process are all dependent on pumps and mixers for efficiency and precision, which are a critical part of ensuring a quality product and sustainability of production. Ingersoll Rand’s ARO, Milton Roy, Albin Pump and SEEPEX pump portfolios include a broad portfolio of progressive cavity pumps, peristaltic pumps, diaphragm and piston pumps, with ARO also offering market-leading diaphragm pump technologies.
Ingersoll Rand offers a wide range of professional services & solutions to suit your exact compressed air needs.